- HOME
- 脱炭素社会への切り札 【次世代パワー半導体】 期待のウェーハ材料 SiCとは
生産現場 計測・検査
脱炭素社会への切り札 【次世代パワー半導体】
期待のウェーハ材料 SiCとは
従来のSiパワー半導体に比較して劇的に電力効率を高められるワイドバンドギャップ半導体。その中でもいち早く量産化が進む、SiCパワー半導体の材料基板技術について解説します。
SiC(炭化ケイ素)は主に人工的に製造されている工業用固体鉱物結晶です。
SiCのモース硬度のモース硬度は9で、炭化ホウ素(9.5)、ダイヤモンド(10)に次いで硬い材料とされています。またSiCは化学的に不活性で安定した物質であり、酸(塩酸、硫酸、フッ酸)や塩基(濃水酸化ナトリウム)にさらされたり煮沸されても高い耐食性を示します。溶解するためには2000度以上の熱が必要となります。
このように高硬度かつ高い安定性をもつ材料ため、従来は粉末や結晶として研磨材として使用されたり、焼結して硬いセラミックスを作ることができることを利用して、自動車のブレーキやクラッチ、防弾チョッキのセラミックプレートなど、耐久性が求められる用途に広く使われてきました。
電子デバイス用途としては、上記の特性を生かして発光ダイオード(LED)や初期のラジオの検出器など、1907年頃に使用が始まり、高温または高電圧、あるいはその両方で動作する半導体電子デバイスに使用されてきました。
従来は、加工および大口径化の難しさから電子デバイス用途としては限られていましたが、Siに対して約3倍のバンドギャップ*¹、10倍の絶縁破壊電界強度*²、約3倍の熱伝導率*³があり、高耐圧が要求される電気自動車や太陽光発電のインバーターにおいて急速に採用が進んでおり、脱炭素社会の切り札として注目されてきております。
Siと4H-SiCの性能比較
Si | 4H-SiC | |
---|---|---|
Bandgap (eV) | 1.12 | 3.26(バンドギャップがSi比約3倍) |
Electron mobility (cm²/Vs) | 1350 | 1000(絶縁破壊電界強度がSi比約10倍) |
Breakdown voltage (MV/cm) | 0.3 | 2.8 |
Saturated drift velocity (cm/s) | 1.0×10⁷ | 2.2×10⁷ |
Thermal conductivity (W/cmK) | 1.5 | 4.9(熱伝導率がSi比約3倍) |
※上記物性によりSiCデバイスはSi比 10倍の高電圧、100倍の低損失、10倍の高周波動作3倍の高温動作が可能
炭化ケイ素 (SiC) は、単結晶でありながら、Si原子とC原子お互いの位置の組み合わせの違いにより、種々の結晶構造 (ポリタイプ) *⁴が存在します。
正四面体からなるSi-C分子構造の積層順序において、SiC単結晶には200種類を超えるポリタイプがありますが、主なポリタイプとしては、4H-SiC、6H-SiC、3C-SiCがあります。
ポリタイプにより、パワー半導体においては、4H-SiCが使用されています。
4H-SiCにおけるHは六方晶 (Hexagonal)、3CのCは立方晶 (Cubic) を意味します。
SiC原子構造イメージ
Si-C 分子構造の積層配置イメージ
SiC代表的ポリタイプの物性値比較
3C-SiC | 4H-SiC パワー半導体で使用 |
6H-SiC | |
---|---|---|---|
Stacking structure | ABC | ABCB | ABCACB |
Lattice constant (A) | 4.36 | a=3.09 c=10.08 |
a=3.09 c=15.12 |
Bandgap (eV) | 2.23 | 3.26 | 3.02 |
Electron mobility (cm²/Vs) | 1000 | 1000(⊥c) 1200(//c) |
450(⊥c) 100(//c) |
Hole mobility (cm²/Vs) | 50 | 120 | 100 |
Breakdown voltage (MV/cm) | 1.5 | 2.8 | 3.0 |
Drift velocity (cm²/Vs) | 2.7×10⁷ | 2.2×10⁷ | 1.9×10⁷ |
Thermal conductivity (W/cmK) | 4.9 | 4.9 | 4.9 |
Dielectric constant | 9.72 | 9.7(⊥c) 0.2(//c) |
9.7(⊥c) 10.2(//c) |
半導体としての単結晶 SiC の歴史は古く、Geトランジスタが発明された1947年から8年後の1955 年、Lely法(昇華法)によって単結晶 SiC が自然核形成成長により得られたことをきっかけに SiC の半導体利用への研究始まりました。しかし、昇華法よる SiC 単結晶は、大口径化が進まず、また品質問題等が改善されないため、なかなか量産にはいたりませんでした。
そんな中1960年代後半に現在も主流な単結晶Si製造方法であるチョクラスキー法により高品質な半導体 Siウェーハが製造されるようになりました。この技術により、トランジスター用にSiウェーハが採用されるようになり、半導体用途SiC の開発は一度中断されました。
その後1978年に現在も量産のため主流となっている種結晶を用いた昇華再結晶法(改良 Lely 法)が開発され、SiC 単結晶の品質ならびにサイズの向上に目途がたち、再び量産に向けての研究がはじまりました。
さらに1987年にデバイス化に必要不可欠であるエピタキシャル膜の高品質化のブレークスルーとなったステップ制御エピタキシー法*⁵が提案され、良質な半導体 SiC エピタキシャル基板が得られるようになったことで、今日の SiC パワー半導体の研究開発/量産化が可能となりました。
SiC 昇華再結晶法
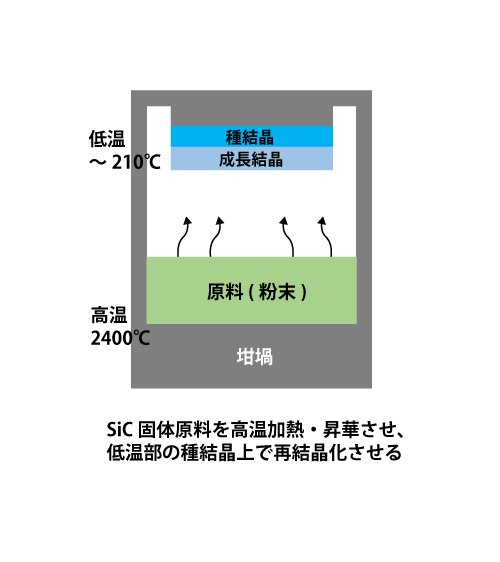
Si チョクラスキー法
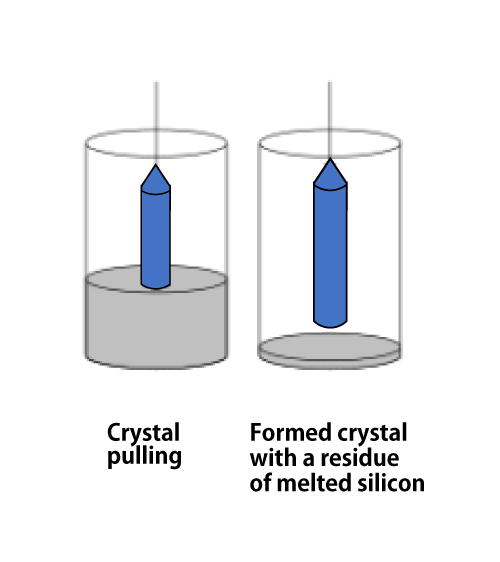
EV向けインバータを始めとする、SiCパワーデバイスの拡大を受けて、SiC基板の生産能力急拡大が進んでいます。2025年には2021年比5倍の約200万枚(6インチ換算)が必要といわれています。
現在のSiC基板製造課題としては主に製造コストと生産の歩留まりの問題があります。製造コストのアプローチとしては、ウェーハ大型化とランニングコストの低減が必要となります。
ウェーハ大型化については、既存の昇華法に加えて、溶液法含む新たなSiCウェーハ製造の研究が進んでいます。SiCはダイヤモンドに次ぐ硬度をもっているため、加工が非常に難しく、時間がかかるうえ研削消耗品のランニングコストもSiに比べて高くなる課題があります。その他バッチ処理による装置大型化の問題、自動化が難しい問題もあり、枚葉処理装置の必要性がでてきます。加えて検査工程の高速化も必要となります。
歩留まりの問題としては、SiC基板結晶成長での結晶欠陥低減、エピ工程でのキラー欠陥*⁶消失が必要となります。そのためにさらなる欠陥の可視化、分類検査が必要となります。
上記のような課題があるなか、SiC需要拡大を受けて、デバイスメーカ各社が基板および、エピメーカと組んで独自の材料基板大型化、高品質化を進めています。
すでに複数社が8インチSiCのウェーハ製造を始めており、さらなる量産性向上と品質向上に取り組み、市場として急速に成長しています。SiCの具体的なデバイス事例については次回以降に解説します。
SiC溶液法図
SiCウェーハ製造工程(装置枚葉化、ランニングコスト低減が必要)
*¹ バンドギャップ:動けない電子が集まっている価電子帯と自由に動ける自由電子が集まっている伝導帯とのエネルギーの差をバンドギャップといいます。バンドギャップが大きいほど、電子の移動に大きなエネルギー(光や熱)が必要となります。金属等の導体はバンドギャップがありません。バンドギャップが小さいほど、熱や光の影響による電子移動が起きやすく、リーク電流の要因となります。バンドギャップが大きいことにより、高温でのデバイス動作が可能となります。
*² 絶縁破壊電界強度:電界を物質にかけた際に、物質が絶縁破壊を起こす寸前の限界値のことです。値が大きいほど物質が壊れにくいことになります。
*³ 熱伝導率:熱伝導率 は、物質内の熱の流れやすさを示す物性値です。熱伝導率が優れているということは、熱を逃しやすく、熱をすばやく放出することができます。熱を逃がしやすいという特徴をもっていると、冷却装置を小型化することができ、回路構成を小さくすることができます。
*⁴ 結晶構造:原子あるいは分子が規則的な配列で結合された固体を結晶といいます。結晶は決まった概形と融点とを持っています。結晶構造とは結晶を構成する、結晶格子の規則的な3次元配列のことです。結晶格子の最小単位は単位格子です。
*⁵ ステップ制御エピタキシー法:結晶表面が(0001)面より数度傾いている面(結晶ステップ)にエピ層をつくる方式で、高品質のエピ層をつくることが可能になりました。1987年京都大学の松波教授の研究室より考案されました。
*⁶ キラー欠陥:デバイスに重大な特性不良を発生させる結晶欠陥の総称です。代表的な欠陥としては、貫通らせん転位、 貫通刃状転位、 基底面転位、 3C 型積層欠陥、 8H型積層欠陥、 キャロット型欠陥等があります。