製品・サービス
異常検知・設備診断システム

CX-Dは、お客様(製造業)の予知保全や品質改善を目的に、設備のデータ収集、可視化、高度なAI技術(機械学習)を活用した異常検知、状態診断が1台のBOX型装置で行える設備診断システムです。設備状態を監視するために必要な機能(データ収集・可視化・異常検知・状態診断・通知・制御など)が標準機能として揃っているため、設備に合わせて設定を行うことで自社の工場に素早く導入し、製造現場のデジタルトランスフォーメーション(DX)の取り組みを前に進めることができる工場のデジタル化ツールです。すべての処理を工場内で完結させるエッジコンピューティング型のシステムです。
概要
異常検知・設備診断システム CX-Dとは?
CX-Dは製造現場のデータ活用に必要な機能と高度な機械学習技術を兼ね備えた異常検知・設備診断システムです。「データ収集」「可視化」「異常検知」「状態診断」「通知」の機能を1つの製品で実現できるため、システム開発やインテグレーションの作業を大幅に削減し、素早い導入を可能にします。また、時系列データ分析マシンCX-Mと共にご利用いただくことで、詳細な分析作業からシステム運用までを自社で実現できます。
活用シーン
メリット
異常検知・設備診断システム CX-Dには、3つの利点があります。
1つ目は、工場内の多様な設備、センサと接続しデータ収集すると共に、必要に応じて様々なアプリケーション(BIツール、データベース、クラウド)と連携して利用できる点です。これにより設備の稼働率向上、予知保全、品質改善、異常検知など様々な現場課題の解決にお役立ていただけます。
2つ目は、IT技術やデータ分析の経験や知識がない方でも、現場でご利用いただけるように開発されており、利用者はプログラミングなどの開発作業を行うことなく、GUIの設定作業だけですぐにご利用いただけます。
3つ目は、高度なAI技術(機械学習)が標準実装されており、簡単な操作で設備データを学習し最適な推論モデル(監視閾値)を生成し監視することができます。
>>【特集記事】製造現場の改善プロセスをDX化する新手法とは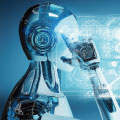
製造業の現場改善は、「生産ロスを顕在化」させることが非常に重要です。こうしたロスの要因を定量的にとらえ、設備の稼動に対する各ロスの影響度を把握することで、課題を明確にし改善を進めていきます。
特徴
1. 多様な設備・センサからの簡単データ収集
プログラムレスで多様な設備・デバイス・センサとの通信、データ収集が可能です。具体的には、ゲートウェイ(Beckhoff、AWS、Azure、FTP等)、PLC(三菱電機、オムロン、シーメンス等)、ロボット、センサ、NC&MCなどORiNが提供する160以上のプロバイダに対応しており、GUIウィザードで簡単に設定するだけでご利用いただるため。導入したその日からデータ収集が開始できます。
2. データを素早く可視化(リアルタイムダッシュボード)
監視対象の設備ごとに目的にあった監視ダッシュボードを簡単(プログラムレス)に作成し、設備の可視化(見える化)が可能です。表示する内容は、設備から収集したデータや異常検知結果、稼働率状況など現場に合わせてカスタマイズが可能です。作成した監視画面は、WEBブラウザでアクセスし閲覧できるため、PCやタブレットからでも閲覧いただけます。また、現場図面を取り組みデジタル情報を合わせて表示するアンドンとして利用することで、製造現場での活用にも貢献します。
3. 異常検知で「いつもと違う」を捉える
CX-Dは、設備状態を監視するための最適な閾値を自動生成するAI機能が実装されています。通常稼働時の様々なデータ(複数項目の正常データ)を機械学習し最適な1つの監視閾値を生成して監視するため、いつもと違う状態になると警告値が上昇し異常検知(変化監視)することができます。本機能により利用者は、従来困難であった設備毎の多種多様なデータ監視が可能となり、設備の異常検知、予知保全の実現や品質改善への役立てるアクションへとつなげることができます。
4. 高度な状態診断(外れ値・多値判別モデル利用)
時系列データ分析マシンCX-Mを活用すると、時系列データを分析、学習して作成した多様な推論モデル(AI)をCX-D上で動作させ、より高度な異常検知(外れ値)や正常・異常判別を行うこともできます。これにより、設備・目的に応じて精度の高い設備状態の診断や生産品質診断などのシステム化を開発作業なく実現できます。
※予知保全や品質改善を目的に、設備の異常検知、故障予測のための時系列データ分析作業と推論モデル(AI)生成を自動化するマシンです。従来データ分析の専門家(データサイエンティスト)が行っていた分析作業(データ前処理、特徴抽出、機械学習による推論モデル(AI)作成)およびプログラム開発作業を自動化し、素早いデータ活用を実現します。
5. 製造現場でも使える直観操作
CX-Dで監視する各設備、デバイスの設定(データ保存・可視化、変化監視(異常検知)、状態診断)は、直観的なGUI画面で設定・管理できます。プログラム開発作業や高度なIT技術は不要です。
6. 多様なアプリケーション・システムとの連携を実現
CX-Dは、汎用のBIツールやリレーショナルデータベース、クラウドサービス等との多様なアプリケーション連携機能が標準で実装されています。これにより既に社内で利用しているツール群を活用しながら、現場課題の解決を進めることができます。各製現場に合わせた監視はCX-Dで行い、工場全体や全社視点で行うデータ活用は、共通ITシステムで行うなど使い分けすることで実用的な投資が可能です。
設備とCX-Dのシステム構成形態
監視対象の設備やセンサとCX-Dは、ネットワーク(Ethernet)で接続します。ネットワークを経由して各設備のデータをCX-Dに収集し、CX-D上で可視化・異常検知・状態診断を行います。監視ダッシュボードは、CX-Dにアクセス可能な端末(PC、タブレットなど)からブラウザでどこからでも確認できます。
他のツールとの比較
CX-D | 一般的なデータ収集システム | |
---|---|---|
システム構成 | 必要な機能が1台に搭載 | 機能ごとに構築 |
データ収集先 | PLC,NC機器多数対応 | 専用装置 |
データ保存形式 | CSVファイル (コピー、取り出しが容易) |
データベース (取扱いに専用知識が必要) |
異常検知機能 | 標準搭載 (数値分布、2項目間相関) |
なし (オプションで追加) |
監視画面 | WEBブラウザ (社内PCのブラウザから接続できる) |
専用ソフトウェア (画面を見るために専用ソフトをインストール) |
監視画面閲覧数 | 255ユーザーまで | 1ユーザー (ユーザー毎にライセンス追加) |
設定変更/画面追加 | 自社内で設定変更できる | 外部発注 |
導入プロセス
製品仕様
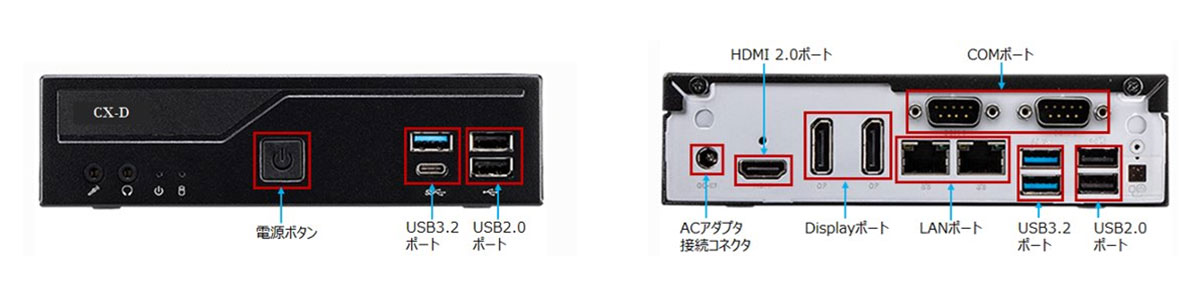
項目 | 製品仕様 | |
---|---|---|
筐体 | スリム型(ファンレス) | |
165(幅)×190(奥行)×43(高)mm | ||
質量 | 1.3 kg (本体のみ) | |
CPU | Intel Core i7-12700 (12コア/20スレッド, 2.1GHz) | |
メモリ | 64GB | |
ストレージ | SSD 256GB(Cドライブ)/ SSD 1TB(Dドライブ) | |
OS | Windows10 IoT Enterprise LTSC 64bit | |
インターフェース | USB | (前面) USB3.2Gen1 ×1 (TypeC×1)、 USB2.0 ×2 (背面) USB3.2Gen1 ×2、USB2.0 ×2 |
オーディオ | (前面) ヘッドホン出力 ×1 、 マイク入力 ×1 | |
カードリーダー | なし | |
無線LAN | (背面) IEE802.11b/g/n/ac | |
有線LAN | (背面) ギガビットLAN ×2ポート | |
映像端子 | (背面) HDMI ×1 、DisplayPort ×2 | |
COMポート | (背面) 2ポート(RS232/RS422/RS485) |
紹介動画
製品ハイライト動画
CX-Dの利用イメージをご確認いただける3分間の動画です。まずはこちらをご覧ください。
製品の詳細解説動画
製造現場の課題から考え、CX-Dをどのように活用してけるかを丁寧に解説していく30分の動画です。しっかり製品を理解したいとお考えの方にお勧めです。
用語解説
予防保全とは
予防保全とは、工場やプラントにある製造装置などの設備に対して、過去の経験を元に使用回数や時間を決めて、あらかじめ部品交換などを行うことにより、故障を未然に防ぐ方法です。また、「TBM(Time Based Maintenance)」と言われる稼働時間に応じて定期的に行われる手法が主流です。TBMは各設備でメンテナンス時期が決まっているため、保全計画を立てやすいという特徴があります。
予知保全とは
予知保全は、工場やプラントにある製造装置などの設備の状態をモニタリングし、不具合や異常の兆候を掴み、それを元に早めにメンテナンスを行い最適な稼働状態を保つ保全の手法です。同義で予兆保全とも言われます。これまでの保全の主流は「TBM(Time Based Maintenance)」と言われる、稼働時間に応じて定期的に行われる手法で行われてきました。TBMは各設備でメンテナンス時期が決まっているので保全計画を立てやすいという長所があります。それに対して予知保全はCBM(Condition Based Maintenance)と言われる、設備や機械の状態に応じて保全を行う手法です。センサやカメラ等で設備からデータを集めて状態を監視・把握し、しきい値を超えるなど異常の兆候がチェックして故障時期を予測し、稼働停止する前に対処します。設備が壊れて長時間の停止を強いられる「ドカ停」を未然に防げるのに加え、設備の状態を見ながら必要な時に必要な設備だけメンテナンスすれば良いので点検回数が減り、総じてダウンタイムを少なくできます。また副産物的に、保守・保全部門の人材不足や技能継承、メンテナンス用部材の在庫最適化と調達コスト削減などのメリットもあります。
推論モデルとは
推論モデルとは「機械学習モデル」を指し、人間が経験を通して学習し判断することをコンピュータで実現するものです。推論モデルは、アルゴリズムを使いサンプルデータを繰り返し解析し規則(ルール)を発見することで作成されます。サンプルデータの量と質が推論モデルの精度の鍵となります。「入力=>推論モデル=>出力」というプロセスで動作し、データを入力しモデルが評価・判定を行い結果を出力します。
エッジコンピューティングとは
エッジコンピューティングとは、データが生成される現場(エッジ)にあるIoT端末やサーバでデータ処理・分析を行う分散コンピューティングです。クラウドへデータを送信せず、エッジでデータの前処理・分析を行うため、リアルタイム性が高く、高いセキュリティを維持し、外部との通信遅延等の影響を受けません。そのため、製造業の工場内でのデータ活用においては、エッジコンピューティングは非常に有効なソリューションとなります。今後、IoTやAIの活用が高度化していく中では、リアルタイムのデータ活用が必要不可欠なため、より多くの分野でエッジコンピューティングへの期待は高まると考えられます。
異常検知(anomaly detection)とは
異常検知とは、一般的には広い意味で異常の発見いうことですが、当社では取得したデータを監視し、一定の観点において、「いつも通りの状態とは異なる」状態を検知する装置状態監視として使用しています。過去に正常稼働したデータから振幅の範囲が大きく外れた場合(外れ値検知)、定期的に繰り返す正常稼働のデータパターンが異なる場合(異常部位検知)、正常に稼働した状態から異なる状態に変化するポイントがある場合(変化点検知)などを捉える方法があります。正常データからの変化を検知するため、異常データがない場合でも装置の状態監視が行えます。
関連製品・サービス
関連記事
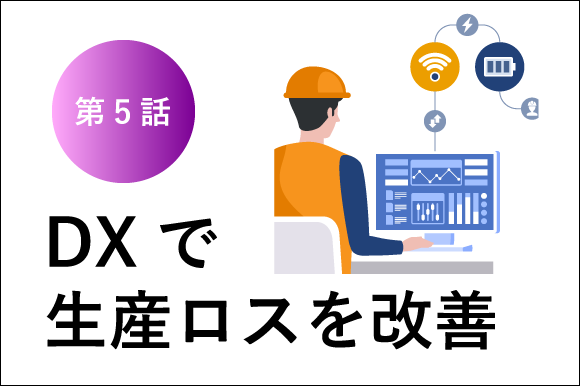
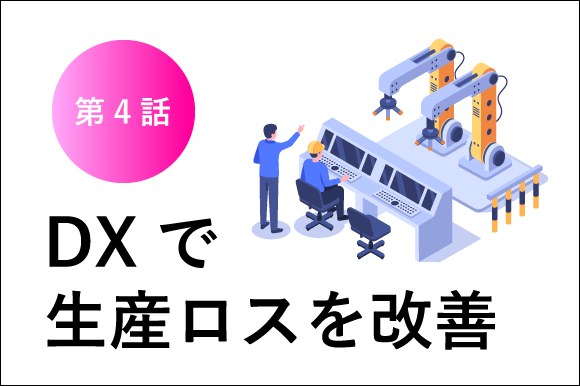
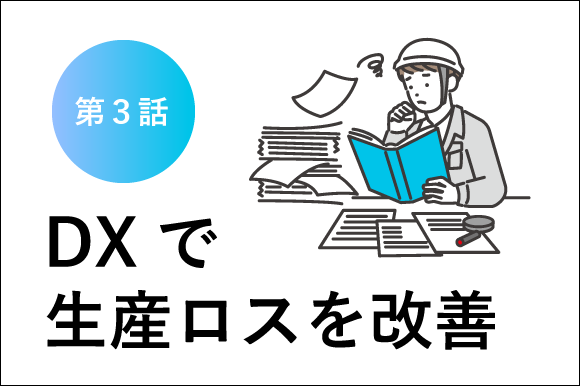
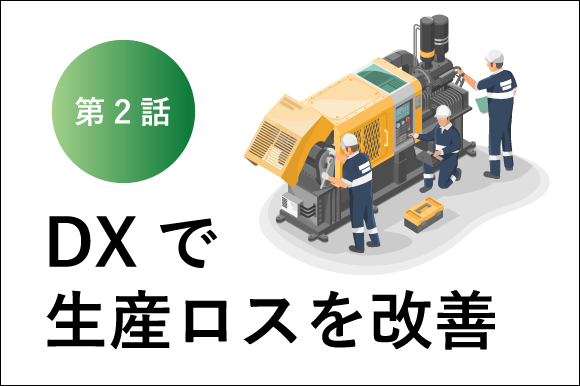
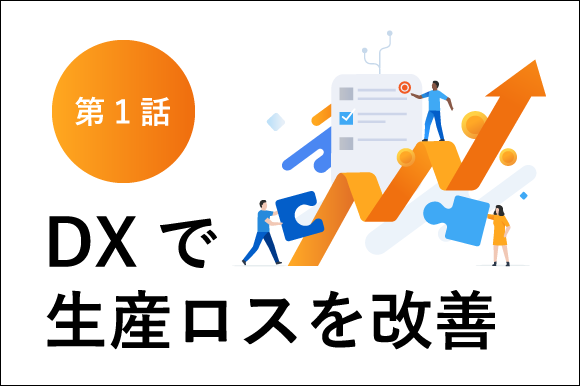
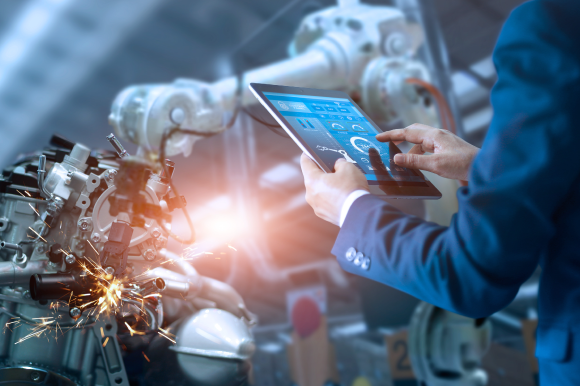
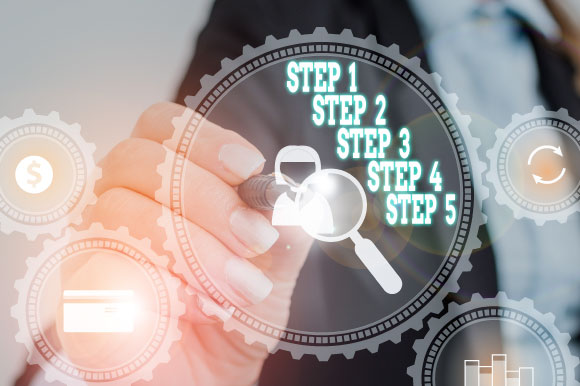
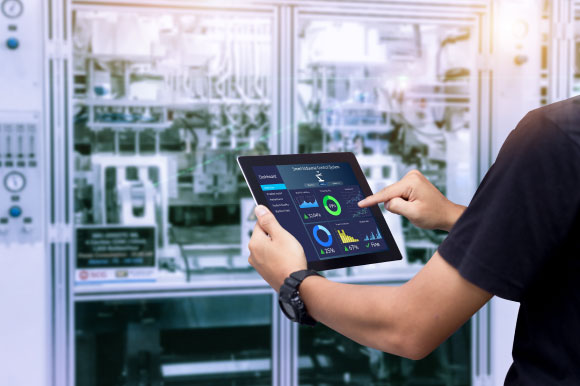
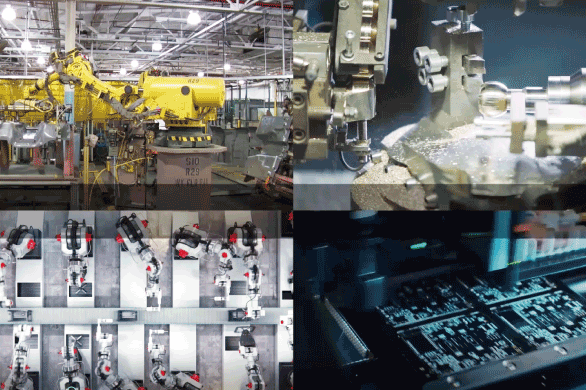
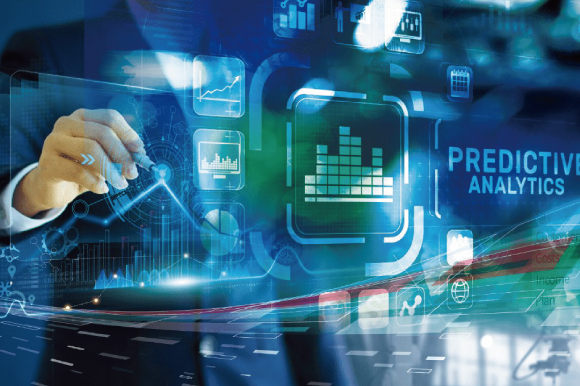
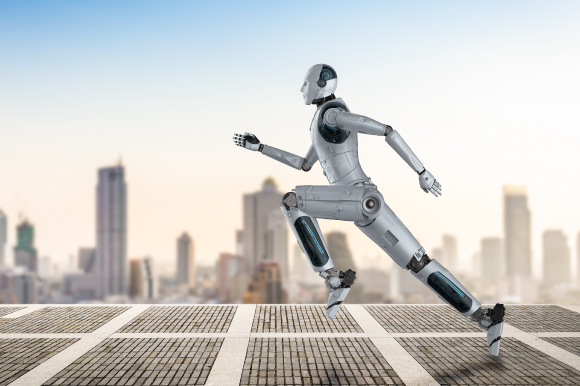
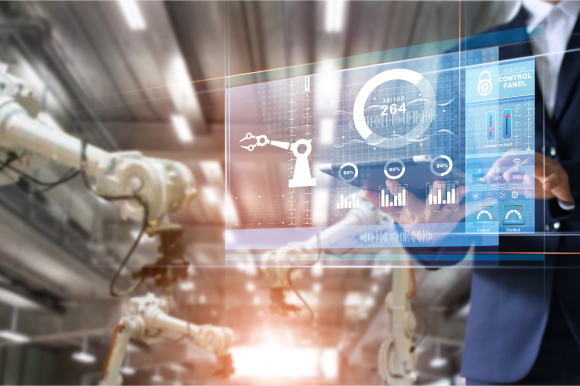
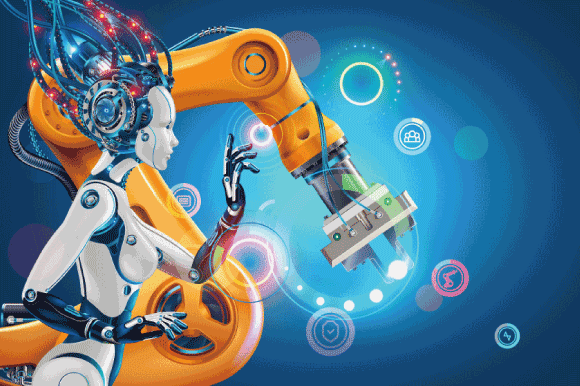
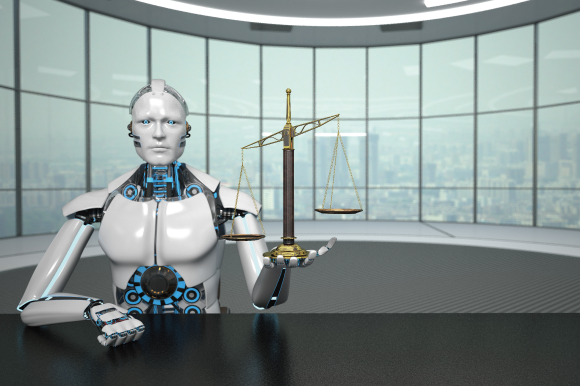
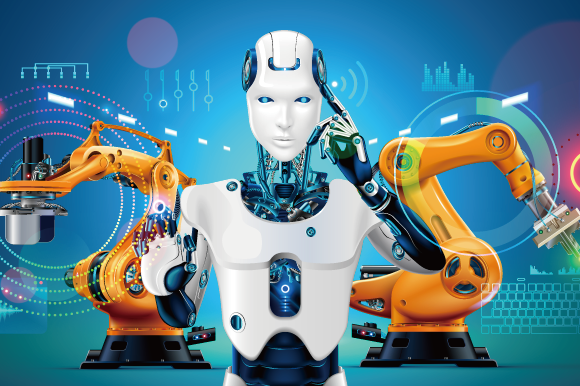
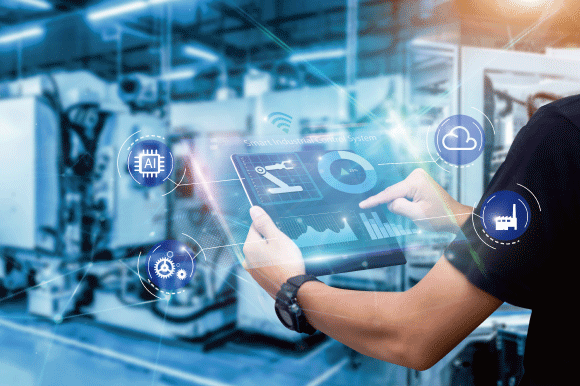
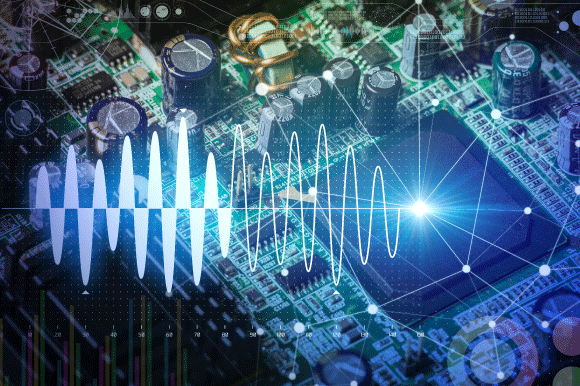
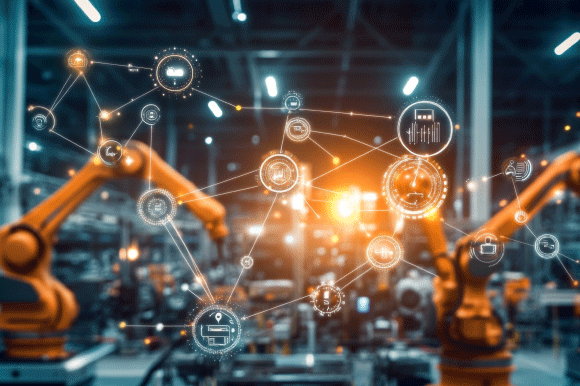
異常検知・設備診断システム 製品外観
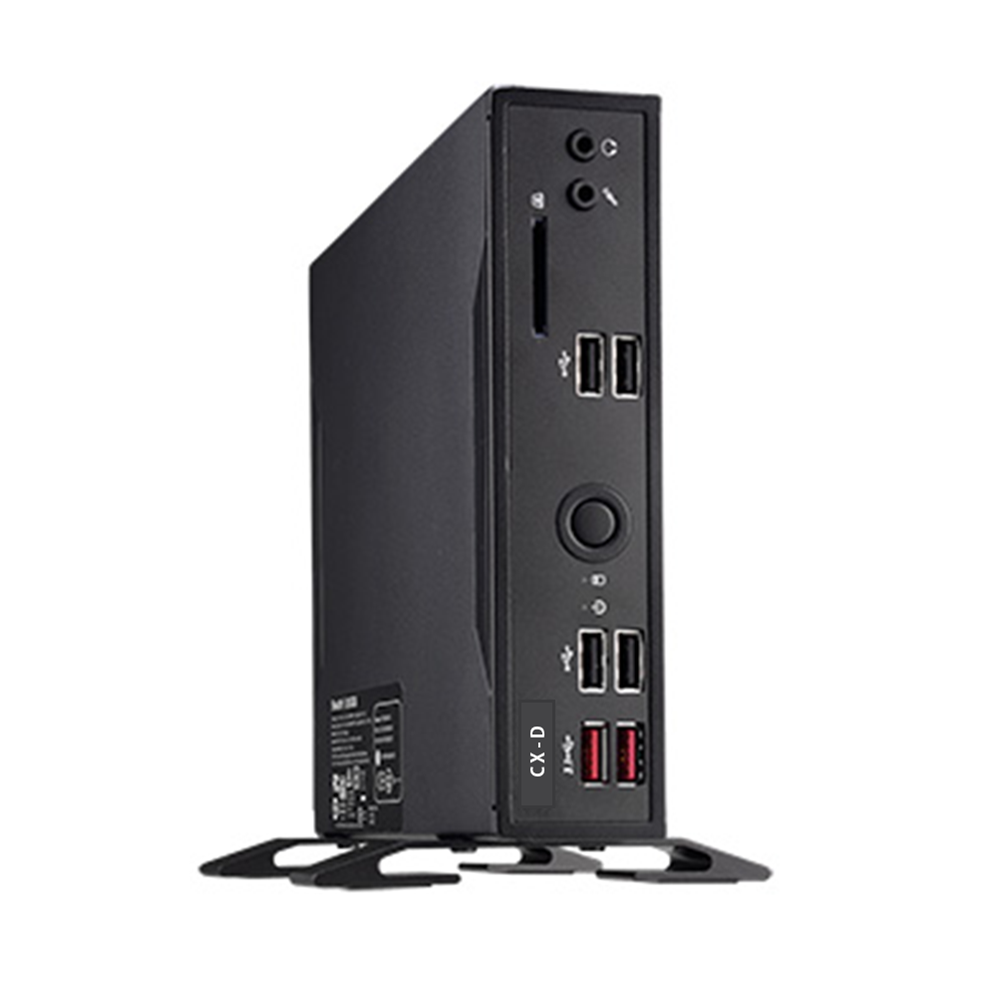
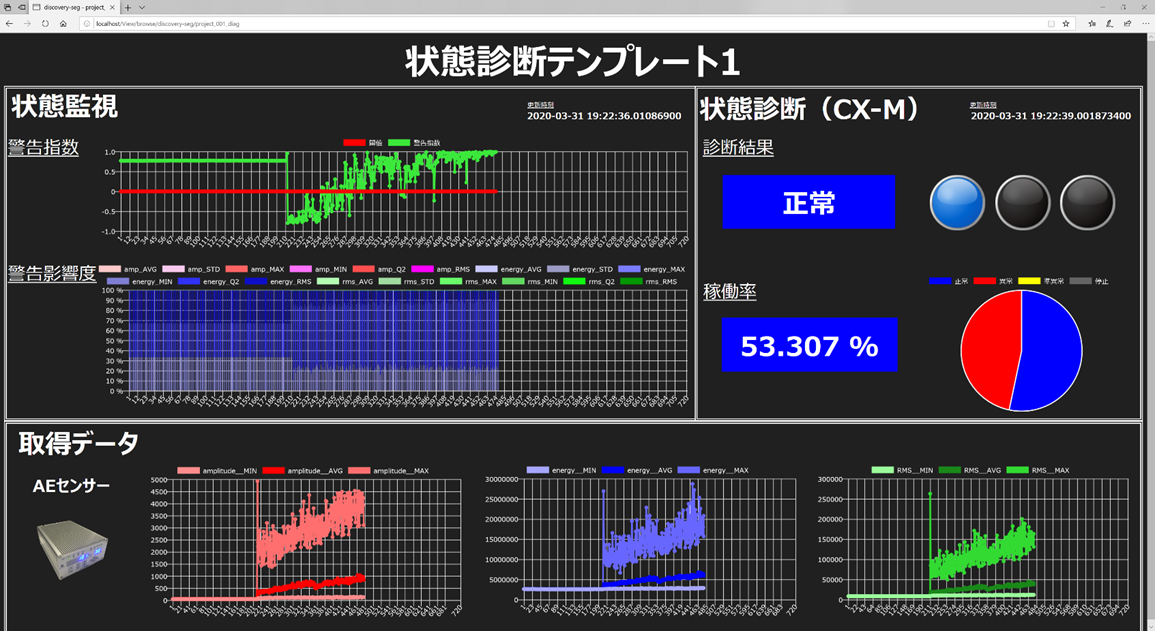
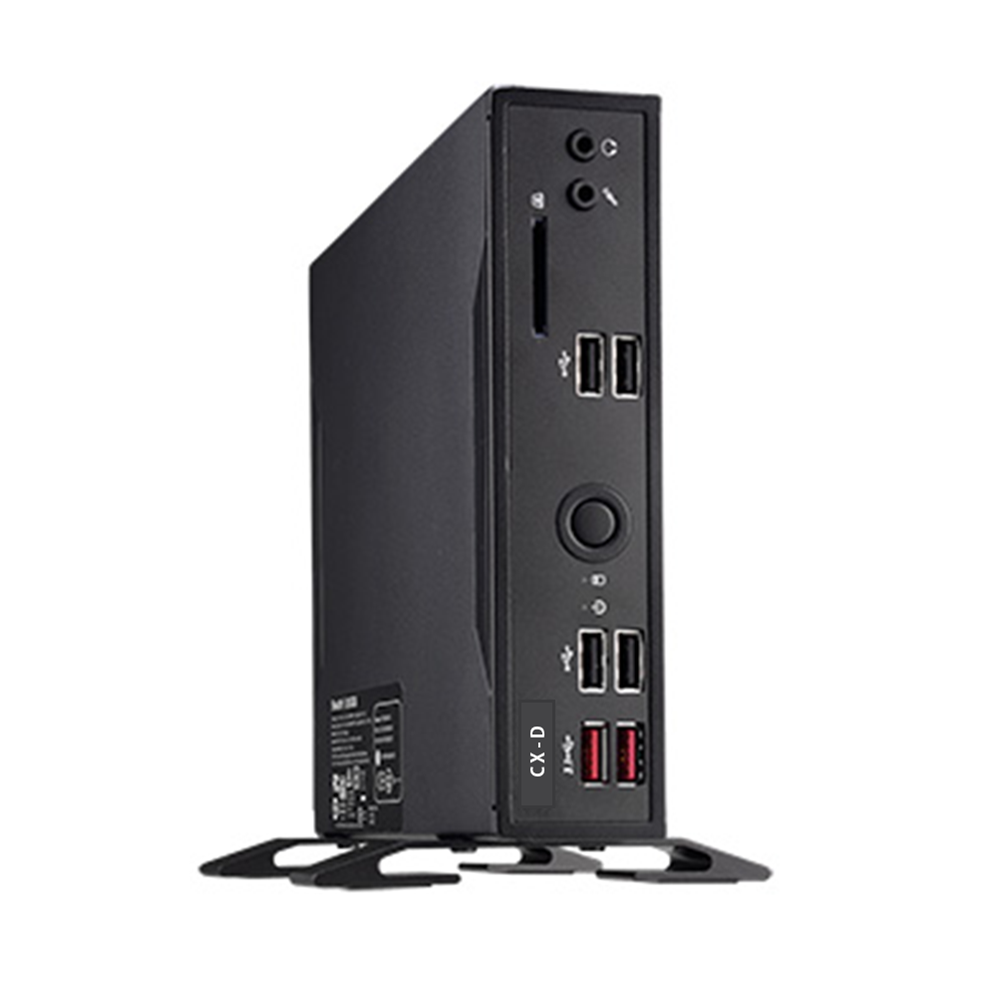
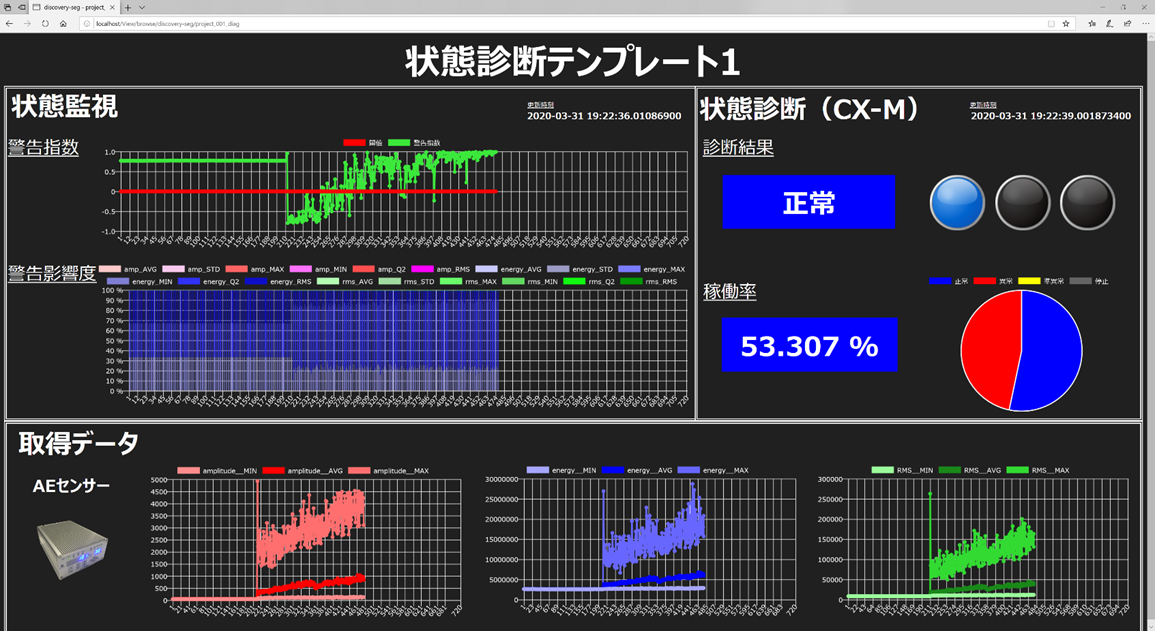