- HOME
- TED長崎のモノづくり 多様化するニーズへの柔軟な対応
設計 設計・製造受託
TED長崎のモノづくり
多様化するニーズへの柔軟な対応
昨今の製品開発においては、ハードウェアからソフトウェア分野にリソースを移行する傾向にあり、これまで自社でハードウェアを開発・製造していたお客様も国内外のEMSへアウトソーシングされるケースが増えてきています。
東京エレクトロンデバイス株式会社(以下TED)のグループに属する東京エレクトロンデバイス長崎株式会社(以下TED長崎)は自社製品の開発・製造のみならず基板設計の受託開発サービスや、基板実装・筐体組立といった受託製造サービスも行っています。
TED長崎は、半導体製造装置組み込み制御ボードのような電子部品のプリント基板への実装、検査と装置の組み立てといったモノづくり(受託サービス)のみならず、電子機器メーカーとして自社製品の開発、設計、製造業務を行っております。
■TED長崎 受託製品例
・エネルギー関連検査装置制御ボード
・半導体製造装置組込制御用ボード
・電力、電源関連計測機器
・ネットワーク関連機器
・水産関連検査装置
・液体測定装置
・公共交通空調制御用ボード
・省エネルギー関連計測機器
・各種産業機器組込コントローラー
また、2017年7月からTEDグループになった事で、TEDが自社開発した製品や受託サービスの製造をTED長崎で行うことができるようになりました。
メッシュ温湿度センサー「ConnecTED TH」
自社製品としては、情報通信機器やスマートエネルギー関連製品を取り扱っています。
例えば電話/FAXとコンピュータを統合したシステム構築の際に必要なCT(Computer Telephony)製品、サ-バやネットワ-ク機器の電源障害、ラック内の温度上昇による環境変化、ドア開閉による外部からの不正操作など、システムの安全運用に必要な環境をリアルタイムに監視するRMS(Rack Monitoring System)製品などといった情報通信機器、蓄電装置や分散電源リソースを使って多様なエネルギーソースを取り込み、系統へやさしく、効率的にエネルギーを貯めて、コントロールする電力変換蓄電装置などを提供しおります。
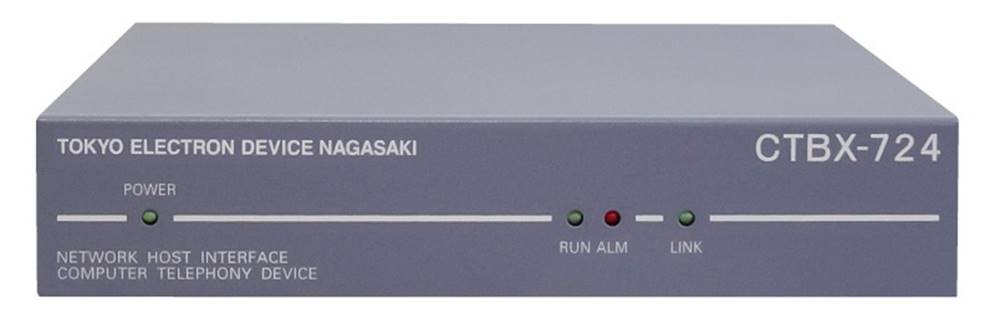
CT-BOX「CTBX-724」
1. 基板実装ラインの特徴
TED長崎の表面実装ラインでは、高集積部品や小型部品の実装を行うため全ラインにはんだ印刷検査機を導入し、画像処理を行い、はんだの厚さ、面積、位置ずれ、ブリッジなどを測定しています。
また、防湿のためのコーティング塗布機がありますので、屋外で利用されるような製品の基板も製造することが可能です。
TED長崎 基板実装ライン
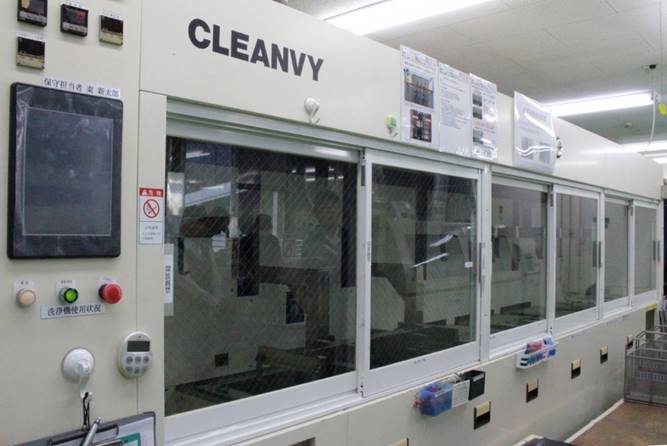
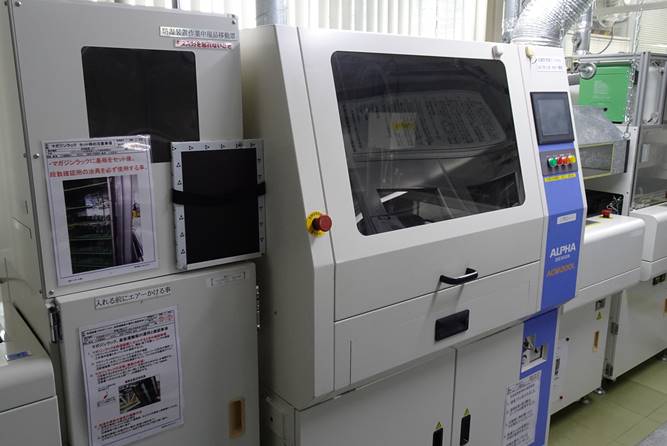
2. 基板検査ラインの特徴
必要に応じて、カメラやレーザー光を用いた外観検査や、X線を用いた実装状態の確認、ICTによる通電検査を行っています。
その他に、ご要望があればお客様指定の検査治具を用いた検査も行います。
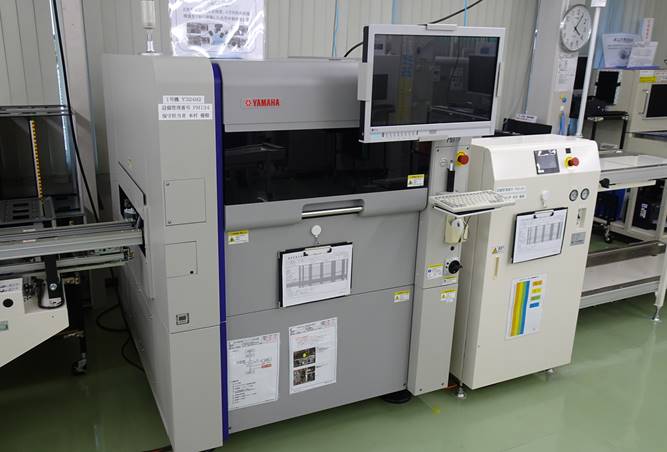
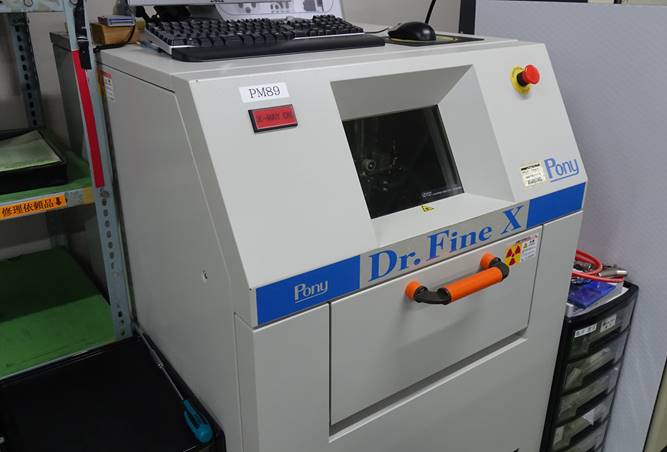
3. その他の設備の特徴
部品の実装に不備があった場合は、リワークを行います。TED長崎では、BGAやCSPといったパッケージ底面の球形はんだボールを端子としている部品などのリワークができる装置を持っていますので、リワーク作業だけを請け負うこともあります。
また、試験環境として恒温(恒湿)室を設置しています。
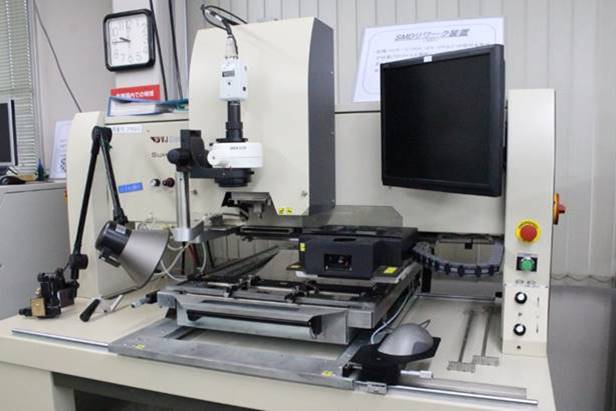

1. 顧客要求に対する柔軟な対応
市場からの要求が多様化している現状から、受託サービスにおいてもそれに対応できる技術や生産体制を持っていることが重要です。
TED長崎は長年、少量多品種の開発・製造を行っており、これまでお客様からの様々なご要望に応えてきました。 MOQ(最低発注数量)については極少量からお受けしており、また、有鉛はんだ対応や洗浄、防湿コーティングなど大手EMSでは手薄な部分に対応する事で付加価値を提供しています。
2. 一貫したモノづくり体制
製品の開発が完了し製造へ移管した際によく起こる問題として、はんだ不良や加工バラツキ、検査での不合格が頻発することなどが挙げられます。これは開発段階での製造意識の欠如によるものが大きいかと考えます。特にこういった事例は開発・製造を外部に委託される際に、より起こり得ることではないでしょうか?
TED長崎では、製造する上で必要な技術要素を取り入れた設計を行うために、設計部門と製造部門が同一箇所に配置されています。それにより両部門が日々密接に関わり合い、互いの技術を融合させる事で、確実な“モノづくり”を実現します。
仕様検討、試作開発、量産製造はもちろんのこと、VE提案や変更通知、不良解析といったアフターサポートに至るまで、TEDグループとして一貫した体制で対応します。
この記事を読んだ方におすすめ!
【設計・量産受託】インテル® FPGAを使用した設計量産受託
【設計・量産受託】部品の生産中止や製造変更での課題とは