- HOME
- 開発者が語る【CX製品誕生の歴史】 製造業のデータ分析作業を変革 時系列データ自動分析マシン「CX-M」の開発秘話
生産現場 予知保全・品質改善
開発者が語る【CX製品誕生の歴史】
製造業のデータ分析作業を変革
時系列データ自動分析マシン「CX-M」の開発秘話
官民を挙げてDX(デジタルトランスフォーメーション)が推進される中、ものづくりの現場でもDXに取り組む必要があります。東京エレクトロンデバイス(TED)では、現場でのデータ活用を推進するためのソリューションとして「CXシリーズ」を開発しています。その一つが予知保全や品質改善を目的に、設備の異常検知、故障予測のための時系列データ分析作業と推論モデル(AI)生成を自動化するマシン「CX-M」です。
なぜ、技術商社のTEDがソリューション開発を手掛けたのか、どのようなコンセプトで開発を進めたのか。担当者に開発の経緯や製品に込めた想いなどを聞きました。
担当者
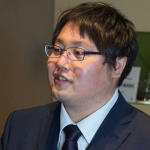
CN BU
アプリケーションサービス開発部
サービスデベロップメントグループ
グループリーダー
岡田大輝
データサイエンティスト。設計、アルゴリズム開発などを担当。
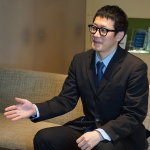
CN BU
アプリケーションサービス開発部
アカウントマネジメントグループ
グループリーダー
高山桂一
課題解決の提案など顧客対応とプロジェクトの進捗管理などを担当。
展示会来場者の声をきっかけに、異常検知のシステムを開発
――技術商社には、電子部品・IT機器などの販売・サポートやソフトウェアの販売・保守サービスを提供するというイメージがありますが、TEDではプライベートブランドとして、生産現場向けの自動化ソリューションや、設計・開発受託サービスも展開していますね。
岡田:当社には企業がIoTサービスを早期に立ち上げるために最適な技術とノウハウをワンストップで提供するIoT設計構築支援サービス「TED REAL IoT」があります。
その中で、「IoTでやってみたいことはあるが、どんなデータを収集すればよいか、取得したセンサーデータを使って何ができるのか」などでお困りの企業をアジャイル型のプロトタイプ開発で支援する「Min Lab」というサービスを展開してきました。
――開発支援型のサービスと、自動分析マシンでは、コンセプトがかなり異なっていますね。
岡田:「CXシリーズ」の開発のきっかけは、2017年に出展した展示会での出来事でした。その展示会では「Min Lab」などの開発サービスをデモンストレーションを通して紹介していました。
そのデモンストレーションを見たお客様から「これで設備の異常を検知することはできるか」という質問があり、「お客様のニーズに合わせてデータ分析を行い、システム開発をご支援します」と対応したところ、お客様はそれ以上の説明を求めることもなく、立ち去ってしまいました。そのとき、お客様が求めているものが「開発サービスでの支援」ではなく「すぐに現場で使えるツール」であることを痛感しました。
高山:開発サービスでは、すばやく「アイデア」を「かたち」にすることモットーにしていましたが、多くのお客様は、すぐに「かたち」を必要としていることを知り、開発不要でお客様がすぐに現場で役立てる製品を作りたいと考え、データから装置状態を診断するための異常判別プログラムを自動で生成できる専用マシン「CX-M」を開発することになったのです。
製造業の現場のニーズに徹底的に応えるシステムへ
――「CX-M」はTEDがそれまでに行ってきたソリューションとは開発の進め方が大きく異なりますが不安は感じなかったのでしょうか。
高山:実は、MinLabというお客様向けの開発サービスは、アジャイル開発というメソッドを取り入れており、短い期間でコアになる機能を開発していく経験を積んでいました。その経験を活かし、きっかけとなった展示会から数カ月後に製品のモックアップを完成させ、これならできそうだという感触を得ました。2017年8月にはプロトタイプも完成し、お客様の一言から始まった開発は、約1年後の2017年11月に「CX-M」としてリリースしました。
岡田:データ分析では、地道に分析のステップを踏み進めて、良い結果を出すのがこれまでの常識でした。しかし、分析のステップを飛び越えて結果が出てくる、つまり“データ分析のステップを自動化させる”、これは想像できませんでした。実際にプロトタイプを見たときには、すごいと感動したのを覚えています。データサイエンティストとしての常識が覆った瞬間でもありました。
――「CX-M」開発では現場のニーズを反映することにこだわったとのことですが、具体的にはどのような点に反映されているのでしょうか。
岡田:IoTサービスではクラウドを使用するサービスが多く提供されていますが、「CX-M」ではスタンドアロンで使用する“BOX型”を採用しました。これは製造ラインのデータを社外のクラウドに保存することに抵抗を感じるお客様が多いことによるものです。いわば小型のデスクトップPCのようなBOX型の場合、問題となるのはリソースが限られてしまう点です。計算処理の負荷を小さくしながら、いかにして精度ある結果を出すか。アルゴリズムの検討では苦労しました。
高山:現場で使うことを考えるとユーザーインターフェースはシンプルである必要があります。マウス操作だけで分析作業が完了できるように、使い勝手には工夫をこらしました。
【操作画面】
分析作業に必要な「データ確認」「判別・分析」「テスト」「特徴抽出」「レポート」「モデル出力」がマウス操作だけで行えます。
リリースはしたものの、お客様の評価は……
――お客様のニーズを反映したパッケージタイプのソリューションとして2017年11月に「CX-M」がリリースされました。お客様の反応はどうだったのでしょうか。
高山:最初の「CX-M」は、お客様が持つ製造装置で採取されたさまざまなデータから、正常状態と異常状態を判別する機能を搭載していました。それには当然、正常時のデータと異常時のデータの両方が必要でした。いわゆる「教師あり学習」と呼ばれるものです。
しかし、リリースをした年の展示会で「CX-M」を見たお客様からは、「異常値が測定されることは滅多にない。限られた環境でしかCX-Mは使えない」と厳しい評価をいただきました。そこですぐに機能追加の開発に着手しました。
それまでの「教師あり学習」に加えて、「教師なし学習」もAIに組み込むことで、正常データの中から外れ値を検出できるようにバージョンアップしました。
―AIの機能追加は約半年で実現しています。その後もバージョンアップを続けています。
岡田:「教師なし学習」のほかにも、さまざまなニーズを反映した機能を追加し続けています。この開発にもアジャイル開発の経験とノウハウが活かされています。実装が可能になった機能から順次、搭載することでいち早くお客様のニーズに応えることができていると感じています。
ひとくちに製造ラインといっても、お客様それぞれで必要としている機能は異なります。お客様がどのような環境で「CX-M」を利用されているのか、そうした背景もしっかりと捉えながら開発に取り組んでいます。
【分析メニュー】
「複数状態の発見と分類」 「正常からの外れ値検出」 「正常・異常を判別」
「複数状態の発見と分類」「正常からの外れ値検出」「正常・異常を判別」と目的にあった分析メニューを用意しています。
【「CX-M」機能追加の歴史】
- 2017年11月28日 「CX-M」の販売を開始
- 2018年6月6日 「教師なし学習」機能を追加2018年8月7日 「マルチソース分析機能」を追加
- 2018年11月13日 「外れ値判定機能」を追加2019年5月9日 「多値判別モデル生成機能」を追加
- 2019年12月12日 「マルチカラムモデル生成機能」を追加
自動化により1カ月かかるデータ分析作業を1週間に短縮
――現場のニーズを反映してバージョンアップを続けている「CX-M」ですが、導入企業の評価はいかがでしょうか。
高山:おかげさまでバージョンアップした「CX-M」はたいへん好評です。データ分析作業の効率化を実現したというお話のほかにも、データを準備するための機能だけでも利用したいといった反響も頂いています。
岡田:データ分析・解析には8つのステップがあります。「CX-M」を使用することで、データの準備やデータを分析する工程の大部分を自動化することが可能になります。
【データ解析・分析の主なステップ】
従来の方法では、採取したデータを分析して、現象を理解し、システム監視するモデルを構築するまでに1カ月ほどかかりました。
「CX-M」は、特徴抽出、要因探索、モデル生成、分析レポートまでが自動化されているので、同じ作業を1週間ほどで行うことが可能になります。
【データから洞察を得るプロセスの違い】
――これまでにどのような企業で「CX-M」が導入されているのでしょうか。
高山:2021年5月までに、約100社に「CX-M」の分析診断サービスを体験していただいています。そのうちの数十社には、実際に「CX-M」導入して、活用していただいています。導入された製造設備は部品加工ラインなどさまざまです。
岡田:新しい機能の追加には手間も時間もかかりますが、バージョンアップを重ねていくうちに、確かな手応えを感じるようになってきました。また、新たにデータを取得したいというニーズが多いことが分かり、データの取得もカバーした「CX-D」の開発につながっています。
後編では、工場現場の設備の状態監視を容易に実現するAIを活用した異常検知・設備診断システム「CX-D」の開発についてうかがいます。
【後編】ものづくり現場のデータ活用を身近に 異常検知・設備診断システム「CX-D」の開発秘話
この記事を読んだ方におすすめ!
~特集記事~
設備診断に有効なAEセンサーとは
予知保全のためのデータ分析ステップとは
予知保全に最適なAIとは?第1弾 “アルゴリズム選択の勘所”
予知保全に最適なAIとは?第2弾 “データ検証で徹底比較”
予知保全に最適なAIとは?第3弾 “AI導入課題と解決方法”
予知保全も時短の時代!?~異常検知の強化~
~導入事例~
100μsの高速AEモニタリング環境でCX-Mによる良否判別を実現、品質確保に活用!
振動データの整理・分析・比較作業を大幅に改善
製造現場の品質管理を自動化!インラインでの品質判定で不良流出0を実現へ
製造現場における「データ収集」と「データ分析」の間にある見えない壁を、シーケンサを活用して突破!
切断機の加工時のデータから不良品をいち早く検知!「加工」と「検査」を同時に行うインプロセス管理を実現へ